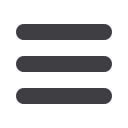
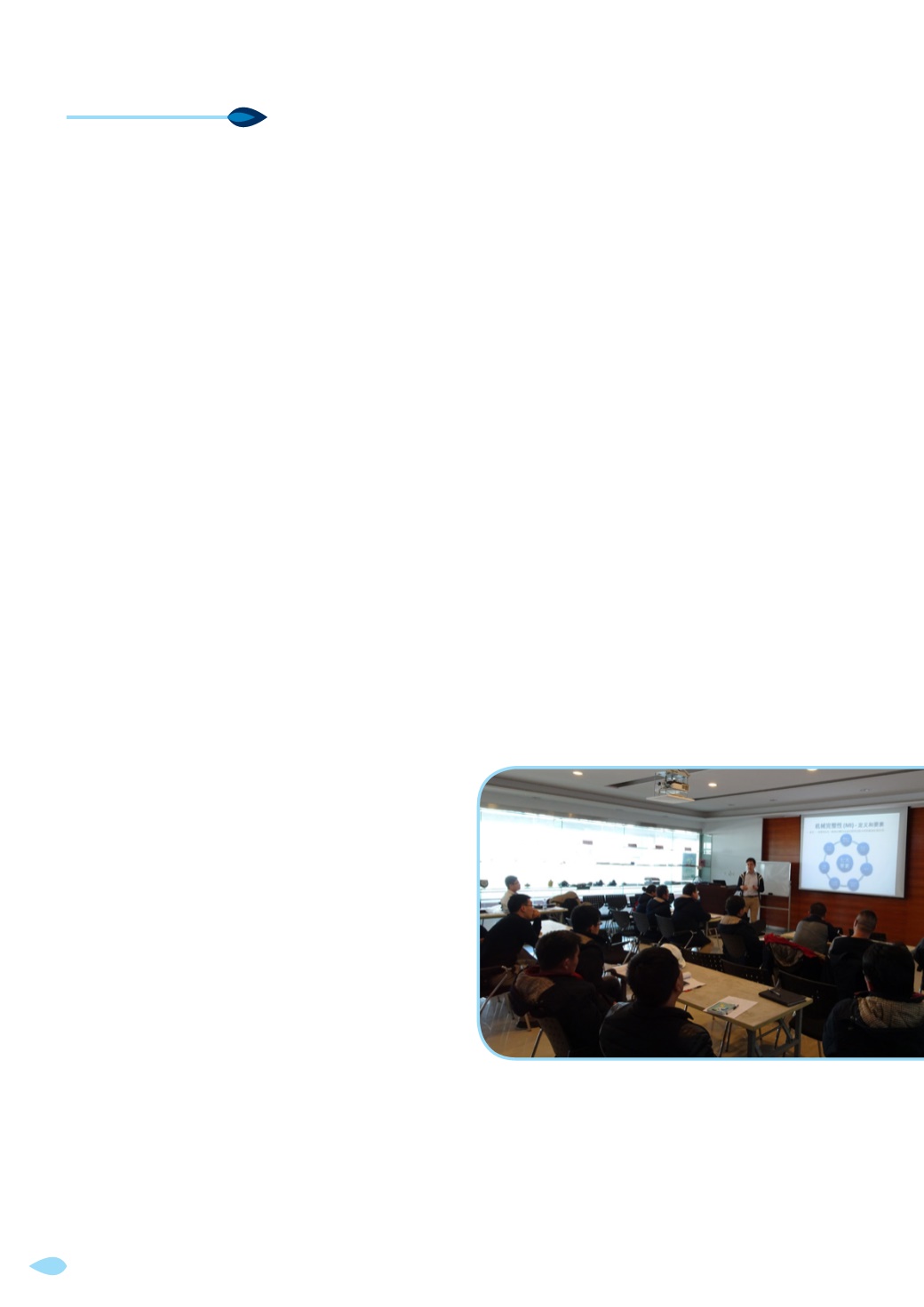
Sustainability Report 2016
56
As a leading energy supplier in mainland China, it
is our responsibility to make safety a top priority
by improving standards within our operations.
We utilise systems that are operationally
successful in Hong Kong, such as SCADA, which
has now been adopted in mainland China.
Likewise, in 2016, we introduced our knowledge
of polyethylene (PE) piping to our mainland
operations and became heavily involved in setting
PE piping standards for the country.
The Group has been asked to become involved in
establishing multiple codes and specifications for
our industry in mainland China, offering a channel
for us to make direct contributions to the gas
industry at large. To help raise the standard of our
industry’s corporate safety and risk management
practices in mainland China, we have published
guidelines such as Towngas Mainland Joint
Venture Network Design, Construction and
Maintenance Guidelines (DM11) and Plant and
Station Equipment and Facilities Maintenance
Guidelines (DM50), among others.
Since 2015, G-Tech Piping System (Zhongshan)
Company Limited, our wholly-owned subsidiary,
has supplied piped-gas operators with PE pipes
manufactured under a stringent quality control
system. By ensuring we only use fittings produced
by our business units, we can be confident that
our JVs’ pipes comply with high safety standards.
Not only does this minimise the risk of accidents,
but it also mitigates reputational risk. We have
continuously implemented the replacement
programme of replacing aging cast iron gas pipe
with more durable PE pipe.
A further level of protection is the requirement
that all our city-gas projects conduct safety
inspections of their operational gas networks and
address any issues that arise.
We also established process safety key
performance indicators (KPIs) for our new energy
businesses, specifically our ECO mainland
Mainland China
chemical plants. Furthermore, we update the
process safety audits for our CBM liquefaction
plant and methanol plant regularly, so they
correlate with the latest national and industry
standards. The 2016 safety audits of both plants
achieved a good result.
A further measure was to adopt bowtie analysis
to identify potential risks arising during
operational stages at our chemical plants, and
ways to offset them systematically. Moreover, we
continued to improve Process Safety Management
(PSM) quality in accordance with international
standards. In 2016, we implemented a Mechanical
Integrity (MI) enhancement scheme at two of our
chemical plants, where a Failure Mode, Effect and
Criticality Analysis (FMECA) was carried out to
determine critical equipment with a relatively high
priority. Over 10 pieces of critical equipment were
identified following the MI workshop, allowing us
to optimise our preventative maintenance strategy
more effectively.